Elopak stuurt proactief op productkwaliteit met HAI-software
Elopak stuurt proactief op productkwaliteit met HAI-software
Real-time trending dashboards kwaliteit in productie
“Als je pas ingrijpt als het misgaat, dan ben je te laat. Onze operators moeten al eerder kunnen zien dat er iets mis DREIGT te gaan. Dan kunnen ze voorkomen dat het fout gaat.”
Met dat uitgangspunt zijn ze bij Elopak in Terneuzen aan de slag gegaan. Doel is om operators aan de productielijn beter te helpen vroegtijdig het ontstaan van afwijkingen te signaleren. De HAI trending dashboards voor operators spelen hierbij een belangrijke rol.
En dat blijkt een groot succes, al realiseren ze zich dat dit nog maar het begin is. Want met de nieuwe aanpak zien ze steeds meer kansen om slimmer te gaan werken. Een mooi voorbeeld dus van de “digital factory” in de praktijk.
Hans-Peter Willems en Michael Vermaat van Elopak in Terneuzen geven uitleg.
Real-time trending dashboards
Hans-Peter Willems is Manager Quality Development bij Elopak: de Noorse multinational die met tien fabrieken wereldwijd een leidende positie heeft als het gaat om drankkartons. Drankkartons voor bijvoorbeeld melk of vers vruchtensap. Hans-Peter is hier internationaal verantwoordelijk voor het verder ontwikkelen van kwaliteitssystemen. Elopak werkt met de software van HAI voor product- en procescontroles. Dit gebeurt in haar fabrieken in Nederland, Denemarken, Rusland, Canada en Oekraïne . Het was Hans-Peter die het initiatief nam om samen met HAI de real-time trending dashboards voor operators te ontwikkelen.
Voedselveiligheid topprioriteit
Hoeveel technologie komt er kijken bij de productie van drankkartons voor aseptische of gekoelde dranken? “Meer dan je denkt”, zegt Michael Vermaat, een ervaren Quality Development Engineer in het internationale team van Hans-Peter. Hij speelde een hoofdrol in de praktische invoering van de dashboards in de fabriek.
Michael vertelt dat kleine afwijkingen in de productie van drankkartons kunnen leiden tot serieuze kwaliteitsproblemen. Hun grootste angst is: voedselveiligheid. De pakken moeten niet alleen vloeistofdicht zijn (zodat ze niet gaan lekken), maar vooral gasdicht. Dat laatste heeft immers als risico dat er zuurstof/bacteriële intrede mogelijk is, en dan bederft de inhoud van het pak. Voedselveiligheid is daarom topprioriteit. Reden genoeg dus voor Elopak om er bovenop te zitten. Dit vertaalt zich in het regelmatig meten van sterkte en dimensies, en in vision systemen die continu visuele inspecties uitvoeren. Al die metingen genereren data. En daar bleek de sleutel te liggen voor de oplossing die Elopak heeft gevonden.
Specificatie-grenzen alleen was niet genoeg
Tot voor kort werkte Elopak bij de kwaliteitscontrole vooral met specificaties waar elke individuele meting aan getoetst werd. Daarbij onderscheiden ze drie niveaus. De beste score is “binnen spec”. Dat wil zeggen dat de gemeten waarde valt binnen de toegestane grenzen en binnen de natuurlijke variantie van het productieproces. Daarnaast hanteren ze de zogenoemde “out of control”-waarden. Deze zijn weliswaar nog binnen de toegestane grenzen, maar vallen buiten de normale procesvariantie. Dat betekent dat de operator het proces moet bijsturen. Het derde niveau is “out-of-spec”. Dan ben je simpelweg te laat. Want met out-of-spec-meetwaarden wordt het product afgekeurd.
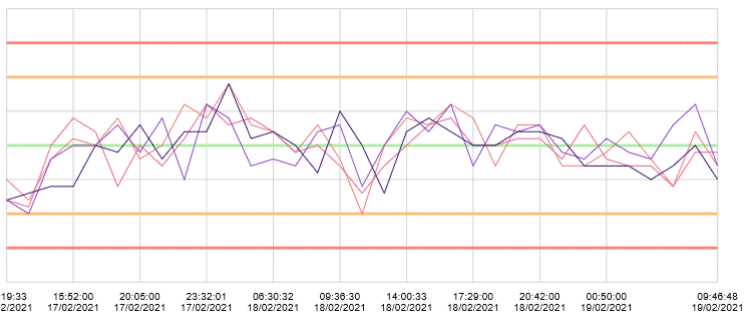
Voorbeeld van een stabiel proces

Voorbeeld van een proces dat dreigt out-of-control te geraken
De oplossing: real-time trending
Dit systeem met specificaties werkt goed, maar met de hoge productiesnelheid geeft het je weinig tijd om het proces te corrigeren. Je bent immers al snel te laat. Liever wil je eerder signaleren dat meetwaarden buiten de gewenste grenzen zullen gaan komen als je niet ingrijpt. Dan heb je immers ruim de tijd om op het proces aan te passen. Het antwoord hierop is: trending. Je laat continu de laatste meetwaarden in een trendgrafiek meelopen tijdens productie. Dan zie je intuïtief wanneer het proces bijgesteld moet worden. Zo kunnen operators proactief werken in plaats van reactief. “Met meer controle en een beter resultaat”, lacht Hans-Peter.
Trending continu in beeld
The devil is in the detail. Dat bleek maar weer toen de trending dashboards op proef in gebruik genomen werden. “Het is cruciaal dat de belangrijkste trends continu in beeld zijn bij de operators”, geeft Michael aan. Maar dat bleek lastig, omdat ze in hetzelfde systeem ook de meetwaarden moeten invoeren. En ze wilden geen extra scherm plaatsen bij de productielijn.
“Dat hebben we opgelost door de HAI-dashboards zo in te richten dat ze na een aantal seconden altijd weer automatisch in beeld komen en real-time worden ververst.
“We willen het de operators immers zo makkelijk mogelijk maken”, geeft Michael aan. En dat blijkt aardig gelukt. Bij de invoering van de dashboards in de fabriek kwamen er eigenlijk geen vragen hoe de trending gebruikt moet worden.
Michael: “het spreekt blijkbaar voor zich. Dat is de kracht van goede visualisaties: een plaatje zegt meer dan duizend woorden.”
De kracht van data
En dit is nog maar een eerste stap. Waar ze naar toe willen is dat mensen op de werkvloer zelf nog veel meer aan de slag gaan met het interpreteren van trendgrafieken. Operators en engineers kennen hun lijn als geen ander. Dus juist zij hebben daarom de hoofdrol als het gaat om het begrijpen wat de data hen vertelt. Daarbij kijken ze niet alleen naar kwaliteitsdata. Want uiteindelijk maak je kwaliteit in je proces, dus is het belangrijk om ook naar de procesdata te kijken.
Juist de combinatie van die twee biedt weer veel nieuwe inzichten. Daarmee proberen ze te leren van historische data. Terugkijken is waardevol. Vooruitkijken nog meer. Zo is Elopak alweer bezig met de volgende stap: op het gebied van machine learning waarbij je aan de hand van data kunt voorspellen wat er gaat gebeuren.
Michael: ”Ook daarover zijn we in gesprek met HAI. Over hoe zij ons daarin kunnen ondersteunen. Het is prettig om samen te werken met een partner die luistert naar onze behoeften en daar ook werkelijk invulling aan geeft.”
Laat je inspireren
Benieuwd naar nog meer praktijkvoorbeelden van slim gebruik van fabrieksdata, speciaal in de food en paper industrie?
Laat je inspireren door successen van anderen op het gebied van OEE, kwaliteit, vrijgave, golden batch, CIP-reinigingen, operator ondersteuning, data analyse, in-line meten, fabrieksdashboards, … en nog veel meer.
Mis het niet en volg ons op: