Potatoes in the Cloud:
A data-driven approach at Lamb Weston’s French Fries Factory
Potatoes in the Cloud
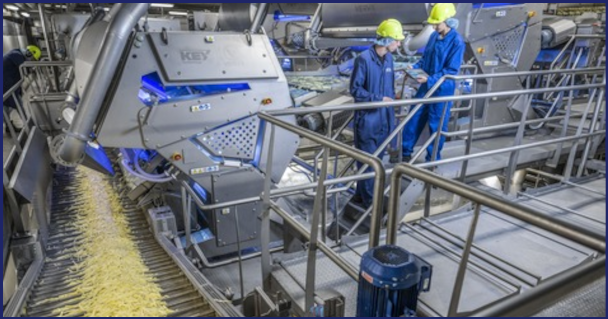
Real-time KPI dashboards in the plant
We’re speaking with Plant Manager Bas van Damme. Together with his team, they’ve defined dashboards that provide operators insights on how to optimally steer the production process. These dashboards are part of the HAI Cloud Platform and use data from Rockwell plant automation, SAP and weighing scales, including data on product quality, and even data on energy and water consumption. All these data is structured and consolidated in the HAI Platform in the Microsoft Azure Cloud. These dashboards offer real-time visibility into calculated Key Performance Indicators, indicating whether adjustments to the process are necessary.
Bas van Damme, Plant Manager:
“If you can increase the yield on the potato and maximize your output, you can significantly boost the profitability of the factory”
Factory Control with varying potato quality
When dealing with a natural product such as potatoes, you face consistently changing raw material quality. This includes factors like potato size, dry matter content, or the number of blue spots. These aspects impact the optimum speed at which a production line can run and the optimum temperature settings.
In the past, the operator determined the optimal process settings based on experience. At least two hours and a lot of manual calculations later, we could see if the settings had yielded the desired result. But by then, roughly 25 to 30 tons of fries would have been processed”, says Bas.
Enhance profitability
With these quantities it is incredibly beneficial to have a real-time dashboard that calculates Key Performance Indicators (KPIs). It allows operators to quickly understand how to make adjustments.
Important KPIs for this plant include Recovery (which is the yield on the potato) and LineRate (the maximum output per hour). “If you can increase the yield on the potato and maximize your output, you can significantly boost the profitability of the factory. That’s why we focus on these aspects” Bas explains.
Challenge us: tell us what you need, and we’ll make it happen
Potatoes in the Cloud
Other information on the dashboards refers to utilities consumption like (bio)gas, electricity, and water. These are crucial KPIs in the context of sustainability, an area of significant importance to the organization. And there are many more plans for new dashboards to come. ‘Digitalization is the future, so we must definitely continue on this path,’ says Bas.
When we look outside, we see that the sky above the Dutch potato fields stretches endlessly, much like the vastness of the Cloud: So bring on more potato data; there’s always room for improvement.
About Lamb Weston
Lamb Weston is a global player in the field of high-quality potato products, where they produce frozen fries in all sorts and shapes that bring joy to people. They also supply semi-finished products for soups, sauces, or mashed potatoes. In the Dutch town of Oosterbierum, about 125 employees work daily to ensure the production of around 2 million portions of frozen fries.
Get inspired
Interested in more best practices of smart use of factory data, especially in the Food Industry?
Get inspired by successes of others when it comes to OEE, quality, positive release, golden batch, CIP-cleaning, operator support, factory data anaytics, in-line measurements, production & technology dashboards… and much more.
Don’t miss a thing, follow us on LinkedIn: