A smart way to manage your digital factory effectively from home
The Covid-19 measures have created a new reality, also for the way factories are organized. For many factories, there is now a minimum of factory personnel on-site. Management and supporting plant personnel work predominantly from home. People working remotely often struggle to stay well-informed on exactly what’s happening in the factory.
When working from home, not only do they miss the opportunity for a quick face-to-face discussion with colleagues on issues as they occur, they often also miss real-time information on production progress, and process- and quality- compliance. Thus, the new reality of factory personnel working from home has intensified the need for cloud plant information systems.
Bernard Marr states in a Forbes article that “companies fast-tracking digital transformation, will be ones ahead of their competition.” With a digital factory people have access to factory and quality information anywhere, any time. Some examples:
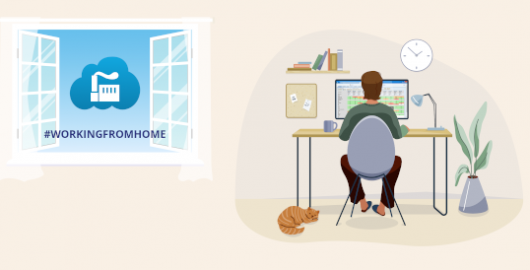
Working from home intensified the need for digital factory software.
Cloud monitoring of plant performance (OEE)
Typical questions on plant performance:
Is the current output as expected?
Do the production lines run well?
If not, what are the problems? How can we solve them?
The HAI software always keeps you connected, also if you are not on-site. And it provides the information you need to support your on-site colleagues.
Cloud monitoring of CCP’s (Critical Control Points)
Typical questions on Critical Control Points:
Are temperatures within specification limits?
Did cleaning take place before production started?
Did operators perform the regular checks on metal detection, hygiene, etc.?
Any deviations?
The HAI software always keeps you connected, also if you are not on-site. And it provides the information you need to support your on-site colleagues.
Cloud monitoring of operator control
Typical questions on operator checks and observations:
Did operators carry out the start-up procedures?
Did they carry out all at-line control points?
Did they perform these checks in time?
Did they record remarks that explain process deviations?
The HAI software always keeps you connected, also if you are not on-site. And it provides the information you need to support your on-site colleagues.
Cloud monitoring of product quality compliance
Typical questions on product quality compliance:
Did plant personnel carry out the necessary product quality control tests?
What were the results?
Did they respond properly to any out-of-spec situations?
Are there any charges in quarantine, why?
Can we release the batches produced?
Did operators record remarks that explain quality issues?
The HAI software always keeps you connected, also if you are not on-site. And it provides the information you need to support your on-site colleagues.
Cloud implementation…. no on-site activities required
To make the HAI software work for your particular plant, we need to connect to your SCADA systems, ERP-systems, lab instruments, etc. Also, we need to configure the software to create operator input screens for operator test results and remarks. When this is finished, we will create real-time dashboards for production personnel, quality personnel, technologists and plant management.
These activities are executed by HAI in a matter of weeks, and remotely. There is no need for us to be on-site for a successful implementation of the HAI software. We have the technology and the expertise to ensure success without actually visiting your factory.
For over 10 years, we have used cloud technology to collect and visualize factory information in real-time. For almost 20 years, we have worked in Food, Chemicals and Bio-technology processes, resulting in best practices for many different processes.
Indeed, we implement the HAI software around the globe without the need for local presence: whether in Saint Petersburg, Amsterdam or Toronto: we get it done, sometimes without even leaving our homes.
Get inspired
Interested in more best practices of smart use of factory data, especially in the Food Industry?
Get inspired by successes of others when it comes to OEE, quality, positive release, golden batch, CIP-cleaning, operator support, factory data anaytics, in-line measurements, factory dashboards… and much more.
Do not miss it and follow us on LinkedIn: