From Data Logging to Data-Driven Decision Making
Pilot HAI Leads to Full-scale implementation across the factory
A pilot project at a manufacturer of ingredients for infant nutrition turned out to be a game-changing success. Automating operator controls not only saved significant time but also provided more reliable data and real-time decision-making insights. An unexpected bonus was improved control over protein content, leading to an annual saving of over €20,000. Enthusiasm among operators, technologists, and managers led to the full-scale implementation of the HAI Data Platform across the factory.
Background
Traditionally, operators spent a significant amount of time manually recording process control data in “hardcopy logsheets.” Following a capacity expansion, the amount of data to be logged increased even further, prompting the search for a solution to automate most of the data registration. Based on successful implementations at other food manufacturers, the company opted for a pilot with the HAI Cloud Data Platform.
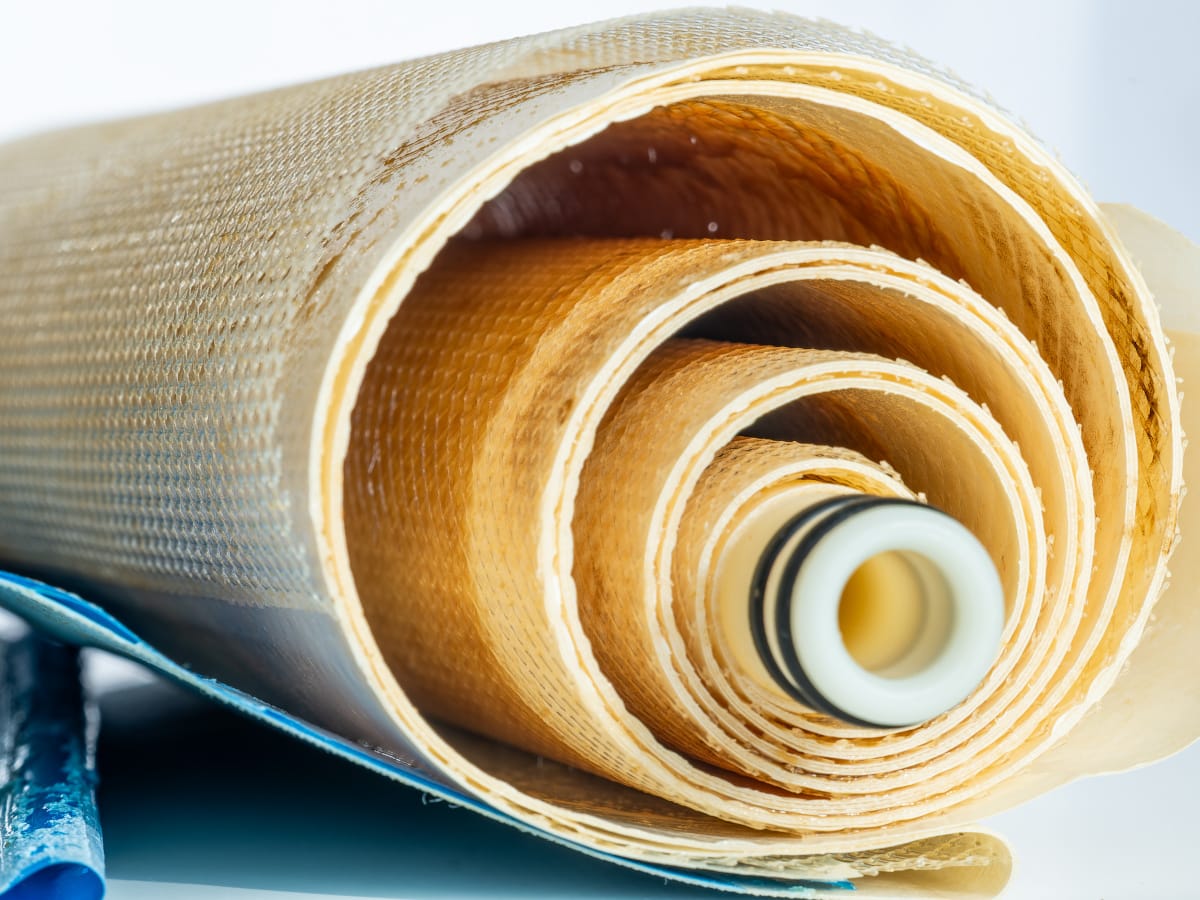
Interactieve NextGen Logsheets
The key driver of success was HAI’s interactive NextGen Logsheets. These logsheets combine automatically collected data (95% in this case) with manual input from operators (now just 5%), all in a single interface.
Additionally, the logsheets assist operators by clearly flagging deviations in critical process parameters.
Operator Feedback After the Pilot
• 100% of operators found that they spend significantly less time logging process data. |
• 82% of operators are enthusiastic about the new approach, stating that HAI provides clear insight into process flow. |
• 82% of operators believe that HAI’s process data-based calculations add value. |
Unforeseen Gain
An unexpected benefit emerged from the smart use of automatically calculated control parameters.
In one of the processes, the protein content in the dry matter of the product is a critical parameter—not only to meet customer specifications but also to optimize process efficiency. Operators typically test a sample from the process at least once an hour and adjust the process based on the test results.
Before implementing HAI, adjustments were made based on the latest test result. However, the HAI logsheets enabled operators to automatically calculate the rolling average protein content in the dry matter for each tank throughout the production run. Instead of relying on the latest individual measurement, operators now adjust the process based on the moving average.
As a result, the variation in protein content in the final product has demonstrably decreased, allowing the specification limit to be lowered. This has led to an annual cost saving of over €20,000 by reducing excess protein giveaway.
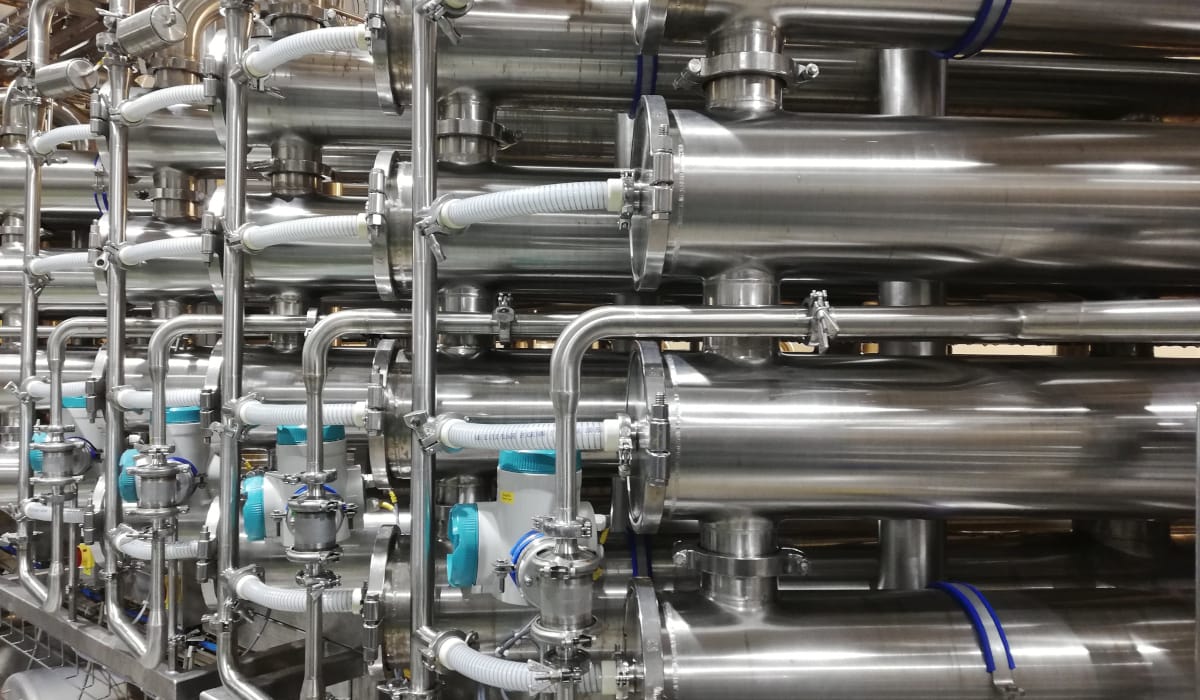
Final Evaluation of the HAI Pilot:
• 100% of the organization believes that process data quality has improved with HAI. |
• 100% of the organization agrees that process data is now more accessible. |
• 100% of the organization finds that investigating process deviations is faster and easier with HAI. |
• 100% of the organization wants to continue using HAI. |
What’s Next?
Due to the pilot’s success, HAI Logsheets have now been rolled out across all departments in the factory. The next step is to integrate data from in-process laboratory measuring instruments directly into HAI Logsheets. This will lead to further improvements, enhancing measurement quality and linking data from the wet and dry stages of the production process.
Get inspired
Get inspired by the success of others in the field of digital transformation, data-driven working and smart use of data (science) in the factory. Also consider applications in the areas of OEE, quality, release, golden batch, CIP cleaning, operator support, trending, Statistical Process Control, in-line measurements, production and technology dashboards, monitoring utilities and sustainability, and much more.
Don’t miss a thing and follow us on LinkedIn: