Digital Shift Handover
Digital Shift Handover drives Production Performance Improvements
Digital Shift Handover drives Production Performance Improvements
Customer interview
“Automated Shift Handovers ensure clear communication and significantly reduce the risk of errors”
What’s the common thread running through Shift Handovers, KPI dashboards, morning meetings, and digitisation?
This connection is evident in an interview with a process manufacturer. For years, they’ve automatically collected and visualized production and quality data in the HAI Cloud Data Platform. With real-time insights and full control, they engage operators daily in the pursuit of operational excellence.
The Production Manager explains how they recently integrated their Shift Handovers into the HAI Data Platform—and how they’ve been reaping the benefits ever since.
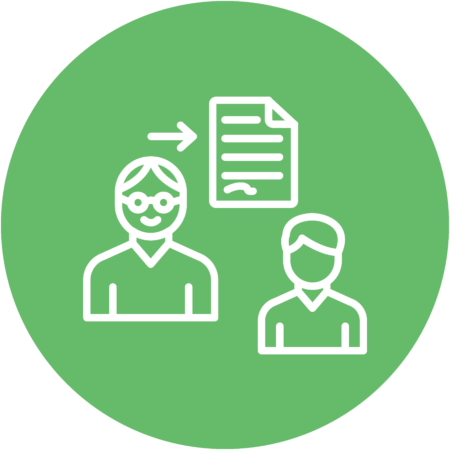
Shift Handover: on paper, in Excel, or custom software?
Factories that operate in shifts have to deal with the handover of tasks from the outgoing team to the incoming one. During this handover, they discuss the current production order, whether the production line is running smoothly, and any other important details. In practice, this handover is often documented—on paper, in Excel or Word, or sometimes in dedicated software systems. Until recently, this manufacturer used such a custom-built system. However, it had become technically outdated and could no longer be used.
From Manual Entry to Automated Reports & Flexible Customization
“All our production and quality data is stored in the HAI Data Platform,” says the Production Manager. This led to the idea of also integrating the Shift Handover process into the same platform. What started as a simple idea evolved into a “kill-many-birds-with-one-stone” project: a significant portion of the shift information is now automatically reported, and supplemented with manually entered data such as explanations and completed checks. This saves a lot of time and reduces the risk of errors. The manager also appreciates the fact that he can adjust the layout and content of the reports himself—without needing help from an IT specialist.
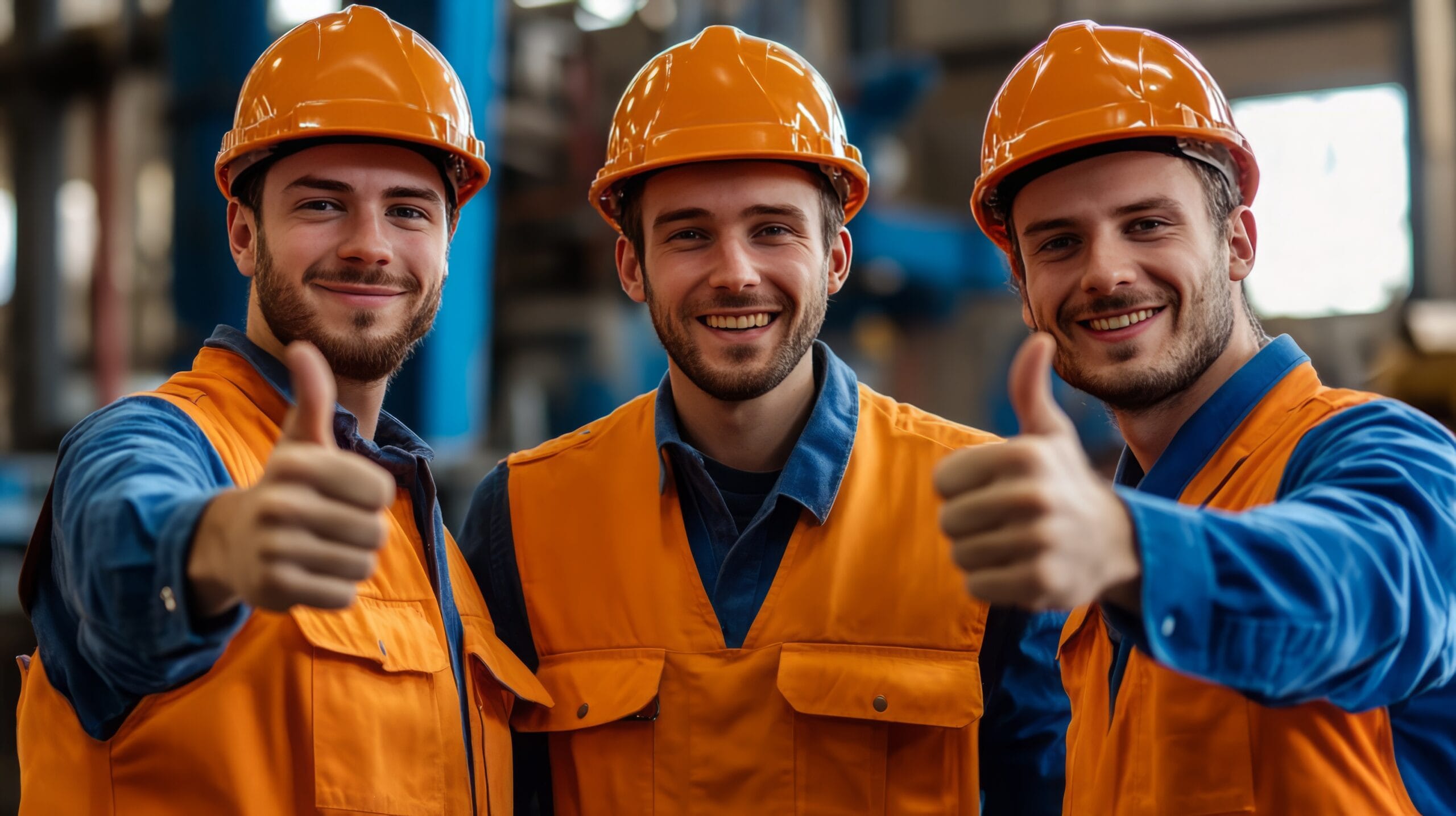
Continuous Improvement
The new system saves time on the shop floor and provides valuable management information that helps trigger immediate corrective actions. The morning meeting is now well-structured and serves as a strong foundation for making decisions—whether it’s addressing breakdowns or adjusting the schedule when production volumes deviate. It also generates input for improvement initiatives. In this way, the new shift handover helps make Continuous Improvement an automatic part of daily operations.
Shift Handover at Department and Plant Level
“We decided to implement Shift Handovers on two levels,” explains the Production Manager. The first level covers individual departments—such as Pre-processing, the Main Process, and Packaging. Operators log completed checks, any notable events, and the nature of breakdowns along with the actions taken.
“In addition, we use a plant-wide shift handover. This aggregates the KPIs from all departments into a single overview, generated automatically.”
This is possible because the HAI Data Platform already contains all relevant information: production orders and batch numbers, data from process control systems, scales, packaging lines, and all quality measurements. And just as importantly: manually entered checks and measurements.
All of this comes together in the shift report, covering Safety, Quality, Critical Process Parameters, Produced and Processed Quantities, Wastewater, and Downtime. Any special notes can be added manually.
The final report is then automatically shared with all relevant stakeholders.
Get inspired
Interested in more best practices of smart use of factory data, in the Food, Chemical and pharmaceutical Industry?
Get inspired by successes of others when it comes to software to facilitating a data-driven approach, a digital factory with A.I., OEE, quality, positive release, golden batch, CIP-cleaning, operator support, factory data anaytics, in-line measurements, production & technology dashboards… and much more.
Don’t miss a thing and follow us on LinkedIn: